POWDER COATING SERVICES
WHY CHOOSE OUR POWDER COATING SERVICES?
Our precision powder coating services will give your parts a finish that is both durable and eye catching. We use only the highest quality powders from industry-leading suppliers. From wheels and rims to home appliances to playground equipment, our comprehensive powder coating process ensures that you will receive consistent, high quality results, time after time.
We currently utilize three powder coating booths to turn around your parts in a fast and efficient manner. Contact us to find out more and put our powder coating experience to work for you!
POWDER COATING BENEFITS INCLUDE:
- Coating of almost any conductive metal
- Specific Formulations to stand up to your intended use
- Significantly higher durability compared to paints
- Our powders are VOC free
- Powders contain no heavy metals such as lead or cadmium
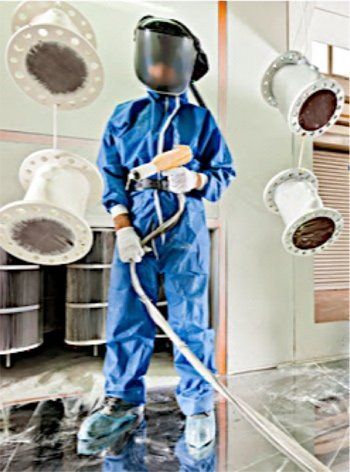
POWDER COATING APPLICATIONS
HOME, AUTOMOTIVE & INDUSTRIAL APPLICATIONS
HOME APPLICATIONS
Powder coating home applications include patio furniture, kitchen tables and chairs, metal cabinets, gas and electric ranges and ovens, shelving, heating radiators, floor vent plates, garden tools, hand railings, wheelbarrows, snow shovels, home appliances, air conditioning condensers, playground equipment, lawn mower decks, and more.
AUTOMOTIVE APPLICATIONS
Powder coating automotive applications include rims, valve covers, race chassis frames and sub-parts, intake manifolds, intake piping, springs, motorcycle frames and sub-parts, hoods, brake calipers, vehicle frames, bumpers, wiper arms, suspension, components, luggage racks, grilles, battery trays and more.
INDUSTRIAL APPLICATIONS
Interior and Exterior Industrial powder coating applications include hand railings, guard rails, posts, metal doors and windows, curtain walls, facades, bathroom fixtures, guardrails, signage, utility pipelines, electrical boxes, lighting fixtures, lockers, motor housings, re-bar and more.
POWDER COATING COLOR OPTIONS
We maintain a large inventory of powder coating powders in stock of hundreds of colors. Custom color matching is also available! With our climate controlled refrigeration room and inventory rotation we ensure that our powder retains the highest possible quality.
SUPERIOR POWDER FOR SUPERIOR POWDER COATING RESULTS
Being proud members of the Powder Coating Institute, we at Van Industries pride ourselves in performing the best possible application for every project! Our powder is only purchased from reputable suppliers that share our vision of excellence.
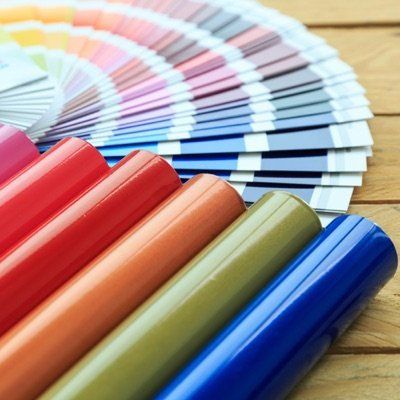
POWDER COATING PROCESS
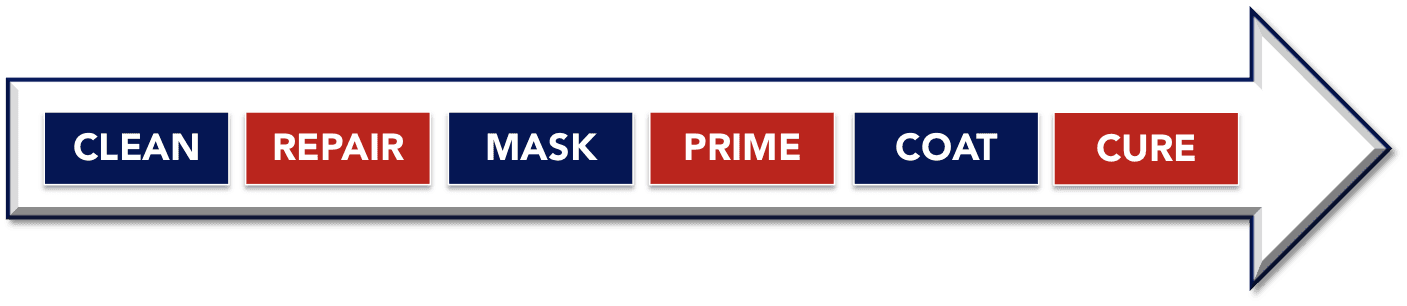
OUR 6-STEP PRECISION POWDER COATING PROCESS
At Van Industries, we pride ourselves on providing the highest quality finish on every project, every time! We regularly consult with our suppliers to ensure that our employees, equipment, and processes exceed expectations in every way. Our powder coating process consists of these key steps:1: CLEAN
There are many critical elements to providing a quality finish, the first among them is providing a clean palette for our powder coating staff to work their magic on. We receive parts in all conditions.
Some parts are rusty, oily, gritty, grimy, some have several layers of paint, some have an old finish that is failing, some look brand new but are not the color of your liking, and some have never been coated. Whatever the condition, our first step is to clean it.
The first step is a very hot oven to loosen any current coatings and impurities.
The second step is an abrasive cleaning process to remove any residual and create an adherence profile without causing any pitting damage. We utilize a number of abrasive cleaning options to ensure parts are cleaned efficiently and the proper surface finish is achieved. Parts are cleaned to SSPC-SP5 (NACE#1) standard.
2: REPAIR
When restoring an old, or weathered part, it is often impossible to assess the full extent of rust damage until after it has been fully cleaned. At this point in the process we often become the bearer of bad news. Although, we can offer some hope..... Our
Welding & Fabrication
capabilities often allow us to repair excessive rust damage. Your Van contact will call you and advise before proceeding.
3: MASK
If, as is often the case, there are sections of the project that need to remain uncoated, such as machined surfaces. Painstakingly, we will mask and/or plug these areas to keep them uncoated. This can take a few minutes or up to hours for more complex parts. An additional part of this process is correctly hanging the part(s). If the part is not properly hung and supported, the end result will have unsightly wire marks. We strive to hang in the most inconspicuous area.
4: PRIME
Once the parts have been thoroughly cleaned, any needed repairs have been made, and their hung, it is time to apply the first layer. Van Industries uses a zinc primer. The purpose of a zinc primer is to aide in protection against corrosion. A powder-based zinc coating will suffice for most applications. However, in working with our trucking industry partners, Van Industries realized that there was a great need for an above and beyond corrosion preventative application protecting parts in the "wet and salty" winter trucking environment. Van worked with a leading coating industry supplier testing a wet-spray coating. It was found that the wet-spray coating provided a superior level of corrosion protection. Van Industries will work with you to find the coating that performs to your specifications.
5: COAT
It takes a skilled hand, proper planning, and proper equipment, to apply a high quality finish. Unscrupulous vendors would have you believe that you can achieve a professional quality powder coated finish with cheap equipment and even cheaper powder in your home oven. If you don't mind hearing, "we told you so," give it a try. We use Nordson Encore LT Electrostatic applicators, (guns), which give the powder a positive charge. The positively charged powder then seeks out a grounded object and instantly adheres to it.
6: CURE
The last step of the coating process is the oven curing. Once the substrate, the part, has been placed in an oven and the part itself reaches the suppliers recommended temperature, for your selected powder, they are fully cured per that powders time duration specification.
This is another area where knowledge and experience come into play. Over curing and under curing both have distinctive effects on the quality and performance of the coating and its finish.
CLICK BELOW FOR THESE RELATED SERVICES: